Graphicast provides essential services and will continue to remain open. Read More.
Innovative, Custom Metal Casting Services
For Better Parts, and a Better Bottom Line
When OEMs and product engineers need metal parts and components, quality, speed, and cost are always a factor. But all too often, they’re forced to make a choice. Quality at the cost of speed? Speed at the cost of quality? Quality and speed at the cost of the bottom line?
At Graphicast, we make it our mission to offer it all: better parts, with a faster turnaround, at a lower cost.
To do that, we’ve spent 40 years innovating the metal casting process through the combination of Zinc-Aluminum (ZA-12) Alloy, our proprietary low-turbulence, auto-fill casting process, and permanent graphite molds ideal for production volumes ranging from 100 to 20,000 parts. Learn more about our low to medium volume manufacturing here.
Contact us today to see if our process will work for your parts, application, or timeline.
Learn What Makes Graphicast a Better Choice for Custom Metal Casting
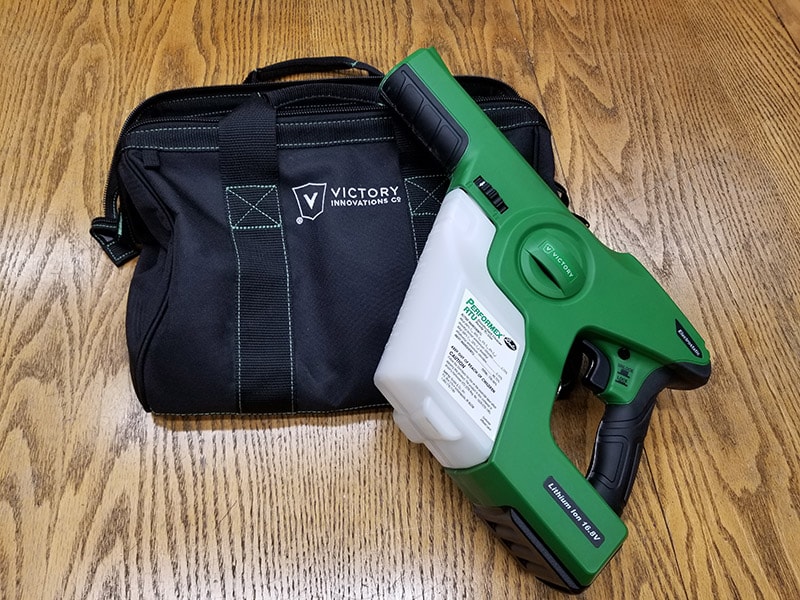
Latest News
Graphicast: Leading the Way in Contamination Prevention Practices During the Era of COVID-19
2020 has been an unprecedented year. As the COVID-19 pandemic continues across the globe, every single person, institution, and company has been impacted. Small businesses like Graphicast, in particular, have faced steep challenges that would have seemed unimaginable only a year prior. While the essential nature of what Graphicast does has ensured that the company […]
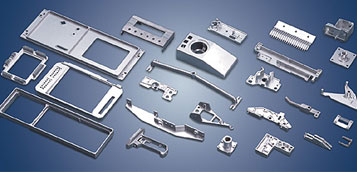
Our Advantage
Better materials, better processes, and better parts means you receive a rapid turnaround and a lower total acquisition cost.
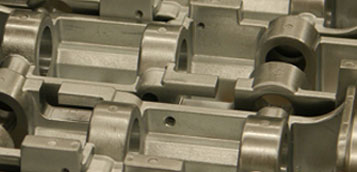
Custom Metal Castings
Graphicast’s innovative process allows for rapid turnaround—going from design to samples in 4 to 6 weeks.
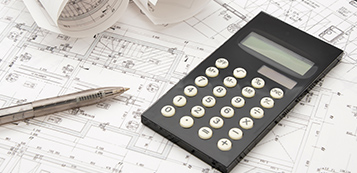
Cost Estimator Tool
Looking for a “ballpark” estimate of costs? We’ve got you covered. Try out our Cost Estimator Tool and see how we can provide a lower total acquisition cost.